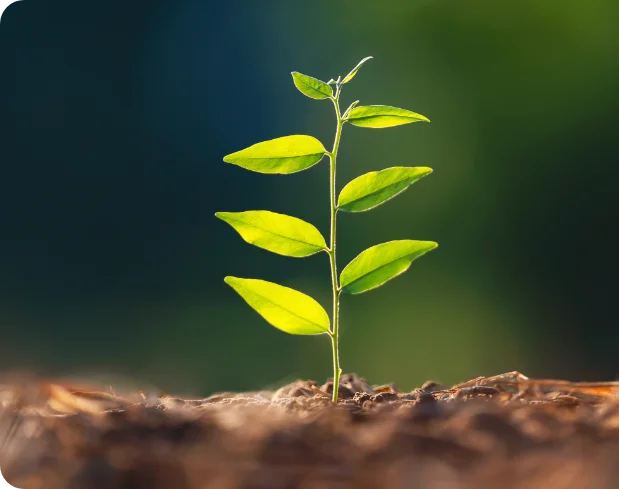
We prioritise
a growth strategy
We are healthcare growth strategy experts, unlike big consulting organisations that alternate between operational and diverse strategy work.
Our commitment to quality is the foundation of our mission to provide safe and effective medicines that enhance lives and promote well-being.
We ensure that products manufactured and distributed by us, consistently meet predetermined quality specifications and our customer expectations.
We stand committed to strictly complying with current Good Manufacturing Practices (cGMP) in conformance with national and international standards. We believe in the continual improvement of our products and processes through training, innovation, and active involvement of our employees.
Aneta has a well-established Quality Management System ensuring the quality of our products. Our Quality Assurance and Quality Control ensure strict compliance with required quality standards. Our focused approach to quality has been one of the reasons that our stakeholders have entrusted us.
To ensure that all our products meet exact international standards, we attach high priority to maintaining stringent quality Assurance processes at our manufacturing locations.
These checks are positioned at different stages of the manufacturing cycle. Quality Assurance (QA) and Quality Control (QC) teams are empowered to keep a strict check on the products and processes to ensure strict regulatory compliance at every stage. Corporate Quality Assurance also ensures that all manufacturing locations, warehouses, and suppliers are Good Manufacturing Practice (cGMP) Compliant. Vendor qualification and management is one of the most important parameters to ensure in-built Quality in our products.
Continual improvements have been the key to maintaining pace with dynamic cGMP requirements. To ensure that all our products meet exact international standards, we attach high priority to maintaining stringent quality Assurance processes at our manufacturing locations. These checks are positioned at different stages of the manufacturing cycle.
Quality Assurance (QA) and Quality Control (QC) teams are empowered to keep a strict check on the products and processes to ensure strict regulatory compliance at every stage.
Corporate Quality Assurance also ensures that all manufacturing locations, warehouses, and suppliers are Good Manufacturing Practice (cGMP) Compliant.
Vendor qualification and management is one of the most important parameters to ensure in-built Quality in our products. Continual improvements have been the key to maintaining pace with dynamic cGMP requirements.
Our QC professionals are concerned with activities related to the correct receipt, handling, packing, and internal control and release of products.
These activities must be carried out prior to the shipment of goods. Aneta QC team ensures that every single batch is released from our facilities only after the necessary controls have been adhered to.
We are healthcare growth strategy experts, unlike big consulting organisations that alternate between operational and diverse strategy work.
We take great satisfaction in highly innovative answers to challenging issues. We both have a love for using persuasive narrative, solid business arguments, and practical advice to assist our customers develop winning plans and earn the support of their organisations.
We support making decisions based on facts. Our consulting strategy is characterized by insight development and quantitative precision. We are professionals at creating research to support quantitative models, creating projections in cutting-edge and emerging markets, and quantifying the indescribably tough.
Above all things, we place a great importance on cooperation and partnership, and we plan our engagements to be very iterative. We get things going quickly to changing customer demands. Our top executives maintain a high bar for quality throughout our engagements and are actively involved.
Aneta has in place a thorough quality control system and labs that cover every step of the production process, from raw materials to finished products. This involves testing and analyzing raw ingredients regularly and in-process and final product testing to verify that our products meet or exceed regulatory criteria for safety and efficacy.
Raw ingredients and finished products are tested using proven methods and equipment following defined procedures. Physical, Chemical, and Microbiological Tests are performed to confirm that the items fulfill the essential specifications for Identification, Purity, Potency, and Safety.
With the use of dedicated Equipment, Cleaning Methods, and Employee Training, our manufacturing facilities are intended to reduce the danger of cross-contamination. We also check the environment regularly to verify that our facilities satisfy set cleanliness requirements.
We have a comprehensive change control procedure in place that necessitates a full assessment of any proposed modifications to our production processes or equipment. This comprises assessing the possible impact on product quality, followed by validation and testing to verify that the modifications do not have a negative impact on product quality or safety.
For its raw ingredients, excipients, and immediate, Aneta has a stringent vendor qualification and monitoring procedure in place. This includes inspecting raw materials in its well-equipped QC lab as well as analyzing documentation and records of quality control methods supplied by the supplier. Aneta also has a system in place to continuously monitor and assess our suppliers to ensure that they continue to meet our quality requirements. Any non-compliance with raw material quality by suppliers is unacceptable to Aneta.
We have a strong quality management system in place to guarantee that all applicable regulatory standards are met. This involves keeping the necessary licenses and certifications, creating and adhering to standard operating procedures, performing frequent internal audits and assessments, and remaining current on regulatory changes. We also collaborate closely with regulatory agencies to ensure that our quality control methods and products comply with all applicable standards and recommendations.
We collaborate extensively with each client to comprehend their specific quality requirements and to create a quality control strategy that satisfies their objectives. This includes defining important quality traits, creating acceptance criteria, and implementing product-specific testing techniques and processes. We also give our clients frequent updates and progress reports to ensure that they are happy with our quality control systems.